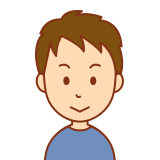
TPMについて詳しくなりたいな、、、。
そんな疑問にお答えします。
☑記事の内容
TPMの心得 第7回
私は自動車メーカーの工場で改善活動の指導を10年以上行ってきました。実績を金額に換算すると1億円以上の改善を行なってきたいわゆる改善のプロです。
そんな私が解説します。
TPMの心得 第7回
- 「ロス」を徹底的に洗い出す
- 洗い出した「ロス」は層別する
- 「ヒトのロス」はIE手法を活用しよう
「ロス」を徹底的に洗い出す
「ロス」とは経営資源であるヒト、モノ、カネ、時間、情報の無駄がある状態です。つまり本来の機能が発揮されていない状態にあるということです。
経営資源の本来の機能を阻害している要因を見つけ出し、排除や予防をしていくことが必要です。
モノの代表である「材料」例に考えてみます。
投入された材料がそのまま100%製品になっていればロスがない状態です。しかし、材料投入時に漏れやこぼれが発生した、生産時に不良が発生して廃棄した、仕上げ時に余分な材料をカットしている、材料保管時に変質して破棄しているなどがあればロスがある状態です。
このような経営資源のロス徹底的に洗い出すことが重要です。
洗い出した「ロス」は層別する
「ロス」を徹底的に洗い出したら層別し、計画的に改善を進めていきます。以下の手順で段階的に層別していきます。
- 16大ロスで層別する
- PQSMDEで層別する
- 課題解決の難易度別に層別する
16大ロスで層別する
16大ロスとは「生産の恋率を阻害する16大ロス」のことです。
この16大ロスの中に「人の効率化を阻害する5大ロス」、「設備効率をを阻害する7大ロス」、「設備操業度を阻害するロス」、「原単位の効率化を阻害する3大ロス」があります。
人の効率化を阻害する5大ロス
- 管理ロス
- 動作ロス
- 編成ロス
- 自動化置き換えロス
- 調整測定ロス
人の効率化を阻害するロスは作業者の動作や作業方法、レイアウトなどによる時間的なロスと本来の作業以外に行う作業の時間的なロスです。
設備効率を阻害する7大ロス
- 故障ロス
- 段取り・調整ロス
- 刃具交換ロス
- 立上がりロス
- チョコ停・空転ロス
- 速度低下ロス
- 不良・手直しロス
設備操業度を阻害するロス
- SD(シャットダウン)ロス
原単位の効率化を阻害する3大ロス
原単位とは物を造るときに必要な原材料やエネルギー、所要時間などのことです。
- 歩留まりロス
- エネルギーロス
- 型・治工具ロス
P・Q・C・D・S・Mで層別する
P・Q・C・D・S・Mとは製造業の6つの生産テーマです。
- P=product 製品・品種
- Q=quality 品質
- C=cost コスト
- D=delivery 納期
- S=safety 安全
- M=morale モラル・意識
これらで層別することで「どんなロスは何に影響を与えているのか」が明確になります。
課題解決の難易度別に層別する
予算、利益、効果での検証を行い、改題の難易度別に送別します。
難易度を効果、予算、実行度等で検討しランク付け等を行い担当者を決定します。
このように層別することでロス改善が具体的な業務として取り組めるようになります。
「ヒトのロス」はIE手法を活用しよう
ロスが顕在化されると「ヒトのロス」も多く出てきます。この「ヒトのロス」にはIE
手法を活用していきます。
IE手法は「方法研究」、「作業測定」といった手法の組み合わせで作業の実態を分析し、具体的な改善点を顕在化する手法です。
「ヒトのロス」によって製品の質や量、コストといったアウトプットは大きく影響を受けます。その「ヒトのロス」の改善の方向性を示してくれるのがIE手法なのです。
IE手法による分析結果は図やチャートで表現できるので、活動版に掲示することで共有化できるメリットもあります。
方法研究とは、「工程分析」「動作研究」「運搬分析」等の手法で分析します。仕事の流れを分析したり、個々の作業の改善に活用します。
作業測定とは、「時間研究」「稼働分析」等の手法で分析します。作業時間を定量的に測定し、現状分析や評価に活用します。
他にも「連合作業分析」、「ラインバランス分析」、「プラントレイアウト」などがあります。これらは方法研究と作業測定を組み合わせた手法になります。
必要に応じて様々な手法を組み合わせて、実態の見える化や改善するべき要因のを的確につかむことが「ヒトのロス」改善には重要です。
まとめ
記事のまとめです
TPMの心得 第7回
- 「ロス」を徹底的に洗い出す
- 洗い出した「ロス」は層別する
- 「ヒトのロス」はIE手法を活用しよう
「ロス」の改善について役立つ心得を中心にしています。
問題=ロスといえるくらいロスは活動に密着しています。
効果的な分析、層別を行って確実な改善を進めていきましょう。
TPM活動の心得はまだまだありますので数回にわけて続けいていきたいと思います。
活発なTPM活動になるよう、心得を全員で共有することも大切です。